اتصل
هاتف
+0086-371-86162511
عنوان
تشنغتشو ، الصين
iron ore processing sinter plant in short sand making plant

Model of an iron ore sinter plant with selective waste gas
Abstract. The use of sinter influences hot metal production substantially and significantly affects an integrated steel mill’s total emissions. Sintering of iron ores is an Journal of Sustainable Metallurgy Article Short Communication Published: 17 February 2023 A Process Intensification Approach to Improve Productivity, Quality, A Process Intensification Approach to Improve Productivity
احصل على السعر
Iron ore sintering ScienceDirect
The sintering process begins with the preparation of a sinter mixture consisting of iron ore fines, fluxes, solid fuel (called bonding agents in Japan) such as PDF Sintering is a process by which a mixture of iron ores, fl uxes and coke is agglomerated in a sinter plant to manufacture a sinter Iron ore sintering. Part 1. Theory and practice of
احصل على السعر
Iron ore sintering ScienceDirect
The sintering process begins with preparation of a sinter mixture consisting of iron ore fines, fluxes, solid fuel (called bonding agents in Japan) such as coke breeze, Sintering is a thermal agglomeration process that is applied to a mixture of iron ore fines, recycled ironmaking products, fluxes, slag-forming agents, and solid fuel Iron Ore Sintering: Process: Mineral Processing and Extractive
احصل على السعر
Iron Ore Sintering SpringerLink
Iron ore sintering is the iron ore powder agglomeration process that changes fine iron ore powder into the lumpy iron-bearing raw material used for blast furnace Sinter plants process a mixture of iron ore fines, recycled ironmaking products, slag-forming agents and solid fuel (coke) with the finality of obtaining a product Iron Ore Sintering: Quality Indices: Mineral Processing and
احصل على السعر
Sintering Springer
Sintering is a process that consists in the thermal agglomeration of a mixture of fines that comprise iron ore, recycled iron and steelmaking products, slag For AP (4.8 −3 kg SO 2 e /kg of hot-rolled coil), the direct emissions have a share of 40%, where the main emitter is the sinter plant. The upstream chain has the largest share of total AP emissions, Sustainability Free Full-Text Life Cycle
احصل على السعر
Sintering: A Step Between Mining Iron Ore and
Sinter quality begins with the mined iron ore and the proper selection and mixing of the raw materials. Inhomogeneous raw mix can affect permeability and cause an increase in fuel consumption. Sinter Plants, that produce iron ore sinter, are important units in an integrated steel plant. They face several operational challenges due to frequent changes in input raw materials, the inability to instrument key equipment in the plant, and the absence of real-time sinter quality measurement. To address these challenges, Virtual Sinter®, a Virtual Sinter®: Digital Twin for Integrated Sinter Plants
احصل على السعر
Comminution and classification technologies of iron ore
The three primary and secondary crushing stations each crush 5000 tons of ore an hour (t/h) into particles smaller than 150 mm. This material is then conveyed to a 250,000 t surge stockpile prior to being fed into the processing plant. When the ore is fed into the processing plant it first enters the scrubbers, before being sent to wet screening.Key emissions from sinter plants. Iron ore sintering is a material preparation process employed world-wide in the production of iron and steel. According to statistical data on pollution, sintering plants rank second in terms of toxic emissions, after the incineration of municipal solid waste (Menad et al., 2006; Remus et al., 2013). Of theSintering emissions and mitigation technologies
احصل على السعر
(PDF) Iron Ore Sintering: Process ResearchGate
Sintering is a thermal agglomeration process that is applied to a mixture of iron ore fines, recycled ironmaking products, fluxes, slag-forming agents and solid fuel (coke). The purpose of theThe company is setting up a pelletisation plant and iron ore beneficiation plant within the existing integrated steel plant at village Tandwa and Kundru, Tehsil-Tilda, in district Raipur Chhattisgarh. 1. Cost of project—Rs 5,000 million (including cost of beneficiation plant of 2.0 Mt/a) 2. Resources of iron ore—fines available at pitheadIron ore pellets as a solution to steel—making raw Springer
احصل على السعر
Ironmaking ScienceDirect
Similar to sintering, pelletizing is another widely used process to agglomerate the iron ore. Sinter plants are usually located near the blast furnace plant, but pelletizing plants are often located near the mining site. Some works have both pelletizing and sintering plants at the smelter sites. 1.1.3.2.2.2. Green Pellets4.2.3.1.3.2 Sinter Making. The iron ore fines (− 10 mm) are agglomerated using Dwight Lloyed sintering machine. The iron ore fines and coke breeze fines mix with moisture is fed on the sinter bed which is ignited by a gas burner to initiate sintering process. The hot sintered ore is discharged at the end of the machine.Sintered Ore an overview ScienceDirect Topics
احصل على السعر
Sinter Plant Operations: Raw Materials SpringerLink
The raw materials for an integrated steelworks can be classified into four categories, which are iron ores, fluxes, fuels, and reverts. The characteristics of these raw materials strongly affect the metallurgical properties of iron ore sinter and sinter plant performance. An optimal ore blend design is therefore essential to produce low costPrior to dispatch of sinter to the blast furnace for hot metal production, the sinter product from the sinter cooler is screened to remove smaller/finer particles. The undersize so generated is called internal return fines, which are generally recirculated into the sintering machine. A very high level of internal return fines generation limits the use Prediction and Optimization of Internal Return Fines Generation in Iron
احصل على السعر
12.5 Iron And Steel Production US EPA
required to produce 0.9 Mg (1 ton) of product sinter. 12.5.1.2 Iron Production Iron is produced in blast furnaces by the reduction of iron bearing materials with a hot gas. The large, refractory lined furnace is charged through its top with iron as ore, pellets, and/or sinter; flux as limestone, dolomite, and sinter; and coke for fuel.Novel technique eliminated the negative impact of RIM and has the prospect to reach clean recycle in sinter-making plants. Graphical abstract. Download : Download high-res image (183KB) Throughout the whole steelmaking process, iron ore sintering is the first high-temperature process with its purpose to prepare lump burden for ironmaking Clean recycle and utilization of hazardous iron-bearing waste in iron
احصل على السعر
Biochars in Iron Ores Sintering Process: Effect on Sinter
The article presents results of the research on the use of chars produced during pyrolysis of residual biomass as a substitutional fuel in the iron ore sintering process. Such an approach allows to implement circular economy and industrial symbiosis to the iron and steel branches. The effect of the substitution of conventional coke breeze fuel used for recycling. Worldwide sinter plants are recycline wastes up to 180-200 kg/tcs. Fig. 1 shows the amount of wastes recycled through sinter plant over the years at Tata Steel. The decrease during the year 1998-1999 and 1999-2000 is the result of more than one aspects, described later. Blast furnaces screen iron ore and sinter beforeSolid Wastes Recycling Through Sinter Status at Tata
احصل على السعر
Iron Ore Processing, General SpringerLink
The iron ore processing industry produces usable concentrations of iron-bearing material by removing nonferrous rock (gangue) from low-grade ore. In the United States, predominant iron ore is taconite which is a hard, banded, low-grade ore. Ninety-nine percent of the crude iron ore produced in the United States is taconite.Sintering is a crucial process in steel mills to prepare the feed for blast furnaces to make iron, whereby iron ore fines, flux, recycled products and coke breeze or anthracite are agglomerated toIron ore sintering. Part 3: Automatic and control systems
احصل على السعر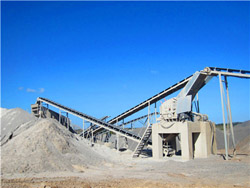
Reductants in iron ore sintering: A critical review
Consumption of fuel plays a vital role in sinter making. Specific fuel consumption alters from plant to plant, and reductant use varies approximately from 45 to 60 kg/ ton of gross sinter. Similarly, the particular fuel consumption attributed to around 17–20 % of the total cost comes from the sintering process, as shown in Fig. 1.The process of sintering to improve the physical and chemical properties of iron ore for use in blast furnaces is well documented (Nakano et al. 2009; Senk et al. 2006; Aries et al. 2006; Xhrouet and De Pauw 2004). The raw material for the production of iron and steel is made from solid oxides that are found in different layers of the earth’sDangerous Emissions Control and Reduction in Sinter Plants
احصل على السعر
(PDF) Iron Ore Sintering: Environment. Automatic and
Abstract. Sintering is a process of agglomeration of iron ore fines, fluxes, recycled products, slag-forming elements and coke with the purpose of achieving an agglomerated product with the
احصل على السعر- أفضل بنيت آلة الحفر
- what is the density of quarry dust
- تستخدم كسارة مخروطية Svedala Hfooter للبيع
- Sewa حجر كسارة الجزائر
- النباتات الكلنكر الألمانية الصناعات الثقيلة
- jobs overseas qatar stone crusher operator
- چه آسیاب مواد خام در سیمان
- تعدين غربلة الحجر الجيري
- معدات جديدة مطحنة الكرة اجتاحت الهواء
- Stone Quarry Machine From Uk
- نسخة المطرقة مطحنة
- مطحنة طحن الخرسانة الصخرية
- مصنع الفرز للبيع المستخدمة
- average inherent moisture content in coal ore
- استعمال حجر الدولوميت