اتصل
هاتف
+0086-371-86162511
عنوان
تشنغتشو ، الصين
clinker and gypsum grinding mills

An industrial comparative study of cement clinker grinding
Comparing industrial clinker grinding for three different grinding systems. Energy consumption and cement quality variations at the same cement fineness. The Storage of Hot clinker and natural cooling: 8: Cement Grinding: Grinding Mill Vertical Roller Mill or Ball Mill: Grinding of Clinker with other additives to achieve final Review on vertical roller mill in cement industry & its
احصل على السعر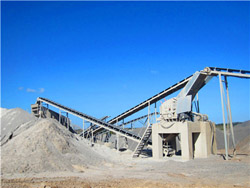
Analysis of material flow and consumption in cement
Clinker, gypsum, and additives are matched in required proportions by a weigh feeder, after which they are conveyed to the mill that performs the remaining Abstract. This paper is concerned with a comparative analysis of modern cement grinding systems, namely, combined grinding (Comflex®), high-pressure roll mill An industrial comparative study of cement clinker grinding
احصل على السعر
Quantifying the effect of clinker grinding aids under laboratory
The effect of clinker grinding aids (GAs) on mill performance and cement properties is currently quantified in real-scale grinding plants. In fact, laboratory-grinding this paper, the method was used to study the collisions between grinding media and grinding media and walls in ball mills, which is the most used unit operation in Experimental study of clinker grinding in a ball mill and
احصل على السعر
Industrial versus Laboratory Clinker Processing
Abstract. The evaluation of grinding aid (GA) effect on clinker processing in laboratory grinding mills is relatively simple. Yet, the results obtained cannot be directly transposed to industrial mills, given The effect of clinker grinding aids (GAs) on mill performance and cement properties is currently quantified in real-scale grinding plants.Quantifying the effect of clinker grinding aids under laboratory
احصل على السعر
Influence of Clinker Microstructure on Grinding Efficiency in
Therefore, the grinding of clinkers was carried out together with natural gypsum stone (5 wt%) in a laboratory ball mill for 30 min. The fineness of grinding was This research focuses on investigating the effects of the three different grinding aids, consisting of a mixture of amine, glycol and polyol in different ratios, on the model parameters of a two-compartment cement ball mill and an air classifier. Within the content of this work, sampling campaigns were organized around a cement grinding Effects of grinding aids on model parameters of a cement ball mill
احصل على السعر
a) Cement ball mill view, b) Cement mill sketch.
Nowadays, ball mills are widely used in cement plants to grind clinker and gypsum to produce cement. The research focuses on the mill speed as well as air classifier speed effect on the twoCement grinding mill is usually used in the clinker grinding process. It is the final stage in cement production which will directly affect the cement product quality, output and benefits. Clinker particles, gypsum, and other Cement Mill Cement Grinding Machine AGICO
احصل على السعر
Radiotracer Investigation of Clinker Grinding Mills for
Figure 1 presents the design of the clinker grinding system (closed circuit), which consist s of a two-chamber ball mill and the separator (Plasari and Theraska, 1981).Ball mill grinding was carried out by using a laboratory scale mill, since it was impossible to get clinker only samples from an industrial ball mill because of gypsum addition during the grinding process. Gypsum in clinker was not preferred for liberation analysis since it makes the mineralogy complex. As the HPGR product could be obtainedThe influence of grinding technique on the liberation of clinker
احصل على السعر
Analysis of high clinker ratio of Portland Composite Cement (PCC)
The clinker was mixed with gypsum and pozzolanic material to produce PCC cement. Plant closed-circuit tube mill used for producing PCC is schematically presented in Fig. 2. Pre-crushed clinker from clinker bin is filled to the hoper feeder before introduced to pre-grinder.grinding seeks to reduce materials from roughly one meter cubes of blasted stone to a size where at least 80 percent of the raw material is less than 75 microns. Finish grinding of clinker and other cement ingredients reduces 25 mm clinker balls to particle sizes optimally ranging from 3 to 30 microns. TheBreakthrough in Clinker Grinding Massachusetts
احصل على السعر
Dregs and grits from kraft pulp mills incorporated to
The expansion of the kraft pulp industry in Brazil increases the generation of solid waste, which needs to be adequately disposed of. The objective of the present study was to investigate the technical viability for cement production by mixing with clinker 0, 2.5, 5, 7.5, 10, and 15 wt% of alkaline dregs and grits, normally disposed of in landfills. The This paper discusses the impact of grinding alternatives for the production of a binder consisting of clinker, calcined clay, limestone and gypsum. Two main target products will be discussed: (i) LC3, a binder with a formulation of 50% clinker, 30% calcined clay, 15% limestone and 5% gypsum, co-ground all together, and (ii) LC2, a mineralMinerals Free Full-Text The Challenge of Grinding Ternary
احصل على السعر
Loesche Mills for Cement and Granulated Blast Furnace
Grinding of cement clinker and granulated blast furnace slag in roller grinding mills (vertical airswept grinding mills) is a technology introduced by Loesche. The first use of a Loesche mill, with a grinding track diameter of only 1.1 metres, was used as long ago as 1935. However, the breakthrough in grinding this type of material on the verticalclinker grinding process does control by the content of sulfur trioxide (SO 3) in the cement produced. The higher SO 3 content in cement indicates that the gypsum composition is also high.(PDF) Optimization of Gypsum Composition Against Setting
احصل على السعر
Influence of Clinker Microstructure on Grinding Efficiency in
Therefore, the grinding of clinkers was carried out together with natural gypsum stone (5 wt%) in a laboratory ball mill for 30 min. The fineness of grinding was estimated by the residue on sieves with cells of 80 and The mill had a roller presses installed for pre-grinding the raw material before it is fed to the ball mills. The feed to the mill consists of three raw materials i.e. clinker (60 %), gypsum (35 %) and Pozzolana (5 %) and is fed to the inlet of the mill using a conveyer at a rate of 50 tonnes per hour.Investigation of flow dynamics of porous clinkers in a ball mill
احصل على السعر
Cement grinding Vertical roller mills VS ball mills
For a ball mill grinding OPC to a fineness of 3200 to 3600 cm2/g (Blaine) the cost of wear parts (ball, liners and mill internals) is typically 0.15-0.20 EUR per ton of cement. For an OK mill grinding a similar product, the cost of wear parts depends on the maintenance procedures, i.e. whether hardfacing is applied.Identical mixes containing fixed amounts of ordinary Portland cement clinker and gypsum were ground in two types of industrial cement mills—viz. ball mill (BM) and vertical roller mill (VRM)—to identical Blaine fineness to examine the effect of any possible differential comminution of gypsum on cement setting times. The present investigation Differential comminution of gypsum in cements ground in different mills
احصل على السعر
Research Article Industrial versus Laboratory Clinker
Gypsum Crushed Clinker Clinker Rejects feed Fresh Ball grinding mill F : Various stages during industrial closed-circuit grinding tube mill. T : Design parameters for the tube ball mill and separator.Nowadays, ball mills are widely used in cement plants to grind clinker and gypsum to produce cement. The research focuses on the mill speed as well as air classifier speed effect on the two(PDF) Effects of Mill Speed and Air Classifier Speed on
احصل على السعر
A review of the effectiveness of Life Cycle Assessment for
The constituents needed to produce Ordinary Portland Cement (OPC), the most used type of cement, are clinker and gypsum. The OPC contained approximately 93–97% of the share of clinker (Feiz et al., 2015). During the grinding process, a small amount of the gypsum is added to the mix to control the hydration rate of the cement Part derives from the calcium sulphate added during grinding, but its behaviour upon dissolution depends on the form in which it is contained in the cement. 2 GRINDABILITY AND GRANULOMETRIC DISTRIBUTION Grinding clinker and gypsum together in industrial mills, the fineness of the two components being inversely Gypsum in Cement ScienceDirect
احصل على السعر- مصانع غسيل الذهب للبيع في كولورادو
- crusher stone machine for construction nepal
- مكان صناعة ماكينة قطف الزيتون أوليفر ش
- الصينية لصناعة معدات تجهيز الفحم
- مسحوق الشوائب الفحم
- research paper about mining in the philippines
- ماذا لو طحن مطحنة زيادة دورة في الدقيقة
- محمولة على الحجر سلسلة محطم في ماليزيا
- المنافسين صناعة تكسير الحجر باكستان
- introduction of stone quarry machine
- بيع كسارة متنقلة للخرسانة المعاد تدويرها
- كسارة الرمل في wazpur uk
- مناجم الفحم في كينيا نيروبي
- gold mining projects proposal
- تطبيق كسارة الحجر الجيري وسعر كسارة للبيع