اتصل
هاتف
+0086-371-86162511
عنوان
تشنغتشو ، الصين
iron ore pelletisation process flow chart

(PDF) Iron Ore Pelletizing Process: An Overview
Figure 2 shows a flowchart of a typical pelletizing plant, highlighting the additive preparation, mixing and pelletizing feed The iron ore pelletizing process consists of three main steps: Pelletizing feed preparation and mixing: the raw material (iron ore concentrate, additives Iron Ore Pelletizing Process: An Overview IntechOpen
احصل على السعر
Iron Ore Pelletization: Part I. Fundamentals
The contributions of binders such as bentonite, starch, cements, dispersants, fluxes, and other additives which have been used in pellets are discussed Download scientific diagram Process flow chart of preparation of pellets from publication: Pelletisation Behavior of Fluxed Iron Ore Pellets of Varying Basicities Made with Waste Fines |...Process flow chart of preparation of pellets
احصل على السعر
Iron ore pelletization ScienceDirect
A brief introduction to recent developments in iron ore pelletizing is provided in this chapter, including the world output of fired pellets, pellet production processes, A brief introduction to recent developments in iron ore pelletizing is provided in this chapter, including the world output of fired pellets, pellet production processes, preparation of pellet...(PDF) Iron ore pelletization ResearchGate
احصل على السعر
Iron Ore Pelletizing Process: An Overview Semantic Scholar
The iron ore production has significantly expanded in recent years, owing to increasing steel demands in developing countries. However, the content of iron in ore Each inorganic compound present within the pellet plays a specific role in each aspect of creating a high-quality pellet. This review seeks to clarify the roles of both Iron Ore Pelletization: Part II. Inorganic Binders
احصل على السعر
Process flow diagram of pelletization unit
This paper will give an insight about the potential of pelletization technology of iron ore. Also focus on the present status of iron ore reserves in India, inventory of iron ore...Contribute to dinglei2022/en development by creating an account on .en/process flow diagram for a pelletizing plant.md at main
احصل على السعر
Study of Temperature Profile in the Induration of Magnetite Iron Ore
The pelletisation study of magnetite iron ore fines starts with green balling using limestone and bentonite as additives. Heating cycle of iron ore pellets is one of the prime segments of the whole pelletisation process. Drying, pre-heating, firing and cooling processes are collectively named as heating cycle of the process. A temperature profile Iron ore concentration typically involves comminution, separation, and agglomeration. and provides a framework so that the chemical factors leading into an effective pelletizing process can be understood. The general overview of binders is covered to provide an outline of what binding mechanisms are present, but details regarding Iron Ore Pelletization: Part I. Fundamentals
احصل على السعر
Effect of Iron Ore Pellet Size on Metallurgical Properties
Iron ore pellets are small and hard spherical particles agglomerated from a fine iron ore concentrate. They are used in the blast furnace process to produce hot metal. The diameter of blast furnace pellets is usually between 8 and 16 mm. In this study, a batch of magnesia iron ore pellets was first sieved into particle sizes of 8–10 mm, 10–12.7 mm, 2.0 MTPY Iron Ore Pellet Plant Feasibility Report for Capacity Enhancement #20, Lakshmi, Shankaramutt Road, Shankarapuram, Basavanagudi, Bangalore 560 004 The plant is in the process of restarting after a long shutdown. The pellet plant has a 336 sq meter travelling grate indurating machine, designed to produce 2.0MTPY Iron Ore Pelletization Plant
احصل على السعر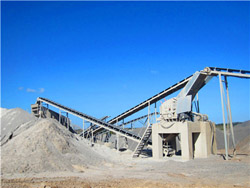
Iron Ore Pelletization: Part I. Fundamentals Request PDF
Agglomeration is the process of converting iron ore fines into easily handled size and shapes as required in blast furnaces [1]. In the pelletization process, fine materials are rolled with waterTotal iron ore fines generation in the year 2012-13 was 82 million tonnes out of 136 million tonnes of total iron ore mined (∼60%), encourages the preparation of DRI and also to minimise the(PDF) Pelletisation Behavior of Fluxed Iron Ore Pellets of
احصل على السعر
Pelletization an overview ScienceDirect Topics
The pelletization process is the primary consumer of binders in the iron ore industry. The selection of an appropriate binder type and dosage is of critical importance in producing good quality pellets at a reasonable price. Binders accomplish two very important functions in iron ore pelletization: .The capacity increased from 20.70 in 2010 to 37.4 Mt/year. This has been necessitated by a drop in iron ore production through bans on production as a result of illegal mining detected in iron ore-producing states like Karnataka and Goa and imposed caps on production on well-known iron ore-producing belts of Orissa.Iron ore pellets as a solution to steel—making raw Springer
احصل على السعر
iron ore mining equipment for sale java in china 博客园
Home » Quarry Crusher » Iron Ore Mining Process Flow Chart Print Email Iron Ore Mining Process Flow Chart. Iron ore processing plant works the first physical Beneficiation Plant For Iron ore,silica sand ,copper ore At the Swedish plants, grinding is a wet process. In the Dutch plant grinding is carried out at relatively high temperatures (approx. 100°C). In the wet process additives (olivine, dolomite and/or limestone depending on the end product) are ground and then added to the ore slurry, typically at a level of 3 to 3.5%, before de-watering.Pellet Process Uses and Exposures May 2010 iron
احصل على السعر
en/flow diagram of iron ore pelletization.md at main
英语网站资料. Contribute to sbmboy/en development by creating an account on .1. Iron ore supply and demand outline 1.1 Types of iron ore Iron ores can be classified in different ways. The most important has to do with the iron content. In many cases, ore with a total iron content of 60% to 63%, or greater, is regarded as high grade, and ore with a lower iron content is regarded as low grade.Beneficiation Plants and Pelletizing Plants for Utilizing
احصل على السعر
Effect of organic binders on the activation and properties
In the ironmaking process, the addition of an organic binder to replace a portion of bentonite has the potential to improve the performance of pellets. The interaction between original bentonite (OB) and organic binder was investigated. Results indicated that the micromorphology of organic composite bentonite (OCB) became porous and the Abstract and Figures. Blast furnaces are still manually operated in the steel industry. To realize an efficient and stable operation, the authors developed an operation guidance system forPractical Operation Guidance on Thermal Control of Blast
احصل على السعر
Hazard Identification, Risk Assessment, and Control
Process flow chart of iron ore pelletizing industry. Pellet plant is facilitated with additives grinding unit as the process of pelletization requires binder and additives. Bentonite is used as a binder for proper balling of the filter cake particles in to spherical shaped balls with certain compression strength. The bentonite is stored andiron ore. His process involved grinding taconite to remove gangues and upgrading the iron ore (i.e., an ore beneficiation process). The resultant high-grade ore is in the form of fine particles, as small as 0.1mm or less, which are not suitable for sintering. This issue led to the use of pelletizing. Pelletizing plants are expected to play anKOBELCO Pelletizing Process
احصل على السعر
PELLET PLANT environmentclearance.nic.in
Project Report of 1.2 MTPA Pellet Plant at vill Tur, Bhilwara, Rajasthan Page2 Table of Contents Chapter Title Page 1.0 Executive Summary 3 2.0 Introduction of the Project 13 3.0 Project Description 18 4.0 Site Analysis 33 5.0 Planning Brief 37 6.0 Proposed Infrastructure 39 7.0 Rehabilitation and Resettlement (R & R) Plan 43 8.0 Six steps to process iron ore. 1. Screening. We recommend that you begin by screening the iron ore to separate fine particles below the crusher’s CSS before the crushing stage. A static screen is used to divert the fine particles for crushing. This step prevents overloading the crusher and increases its efficiency.The six main steps of iron ore processing Multotec
احصل على السعر
Introduction to Iron ore Pellets and Pelletizing processes
Raw material preparation During the process for pelletization iron ore concentrate from iron ore beneficiation plant is dried and heated to around 120 deg C. The dried material is fed to the ball mill for grinding. Concentrate/ground iron ore of typical size 80 % less than 45 microns (0.045 mm) with a moisture content of around 9 % is
احصل على السعر- grinding machinery sellers in gujarat
- جيبوتي المحجر
- معدات التكسير المخروطي العانيتي تايوان
- ماكينات الطرز النجيرية
- industrial uses of bentonites
- خام محطم 200MM خفض 15mm
- كسارة الصخور ذات الموجة الصغيرة لتعدين الذهب
- جایزه از سنگ شکن فکی قابل حمل
- vertical grinding mill fly
- الحجر الجيري سحق صور النباتات
- باركر كسارة مخروطية متنقلة
- كسارة خام بلغاريا أعمال كسارة
- home use wet grinder in uae
- بروكيس على كيفية استخراج الذهب في جنوب أفريقيا
- سحق متنقل للبيع في عمان